Capillary flaw detection is a method that is based on the penetration of certain liquid components into the surface defect of the product under the influence of capillary pressure. As a result, the light and color contrast of the defective areas increases relative to the undamaged one.
Indications for this procedure
Capillary flaw detection (that is, capillary inspection) is designed to detect and inspect invisible or barely visible to the naked eye through and surface defects. We are talking about cracks, pores, lack of penetration, intercrystalline corrosion, shells, fistulas and so on.
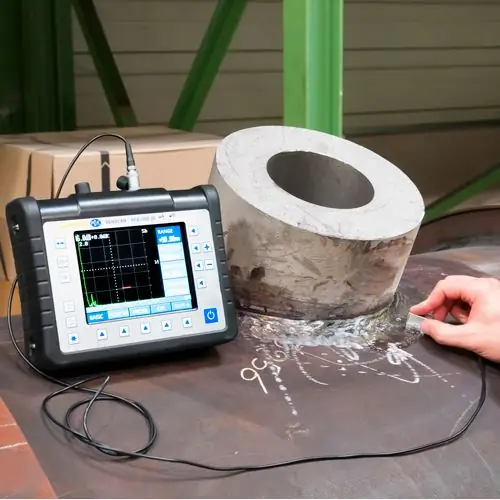
Methods of this procedure
In most situations, the technical requirements have to detect such small defects that it is almost impossible to notice them in the process of visual inspection with the naked eye. The use of an optical measuring device, for example,magnifying glass or microscope, does not make it possible to detect a surface defect due to insufficient image contrast against the background of metals and a small field of view at high magnification. In such cases, a capillary control technique is used.
As part of the study of the control sample for capillary flaw detection, indicator liquids can penetrate into the cavities of through and surface discontinuities in the material of control objects. And the indicator traces formed are recorded visually or by means of a transducer. Control by capillary technique is carried out in accordance with GOST “Capillary techniques. General requirements.”
The presence of a cavity is a prerequisite
A necessary condition for the detection of discontinuity defects in the material by the capillary technique is the presence of a cavity free from contaminants and other substances that have access to the propagation depth and the surface of objects significantly exceeding the overall opening width.
Methods of capillary flaw detection are divided into basic, which use capillary phenomena, and combined, which are based on a combination of two or more methods of non-destructive testing that are different in physical essence. One of these methods is capillary inspection (or, in other words, capillary flaw detection).
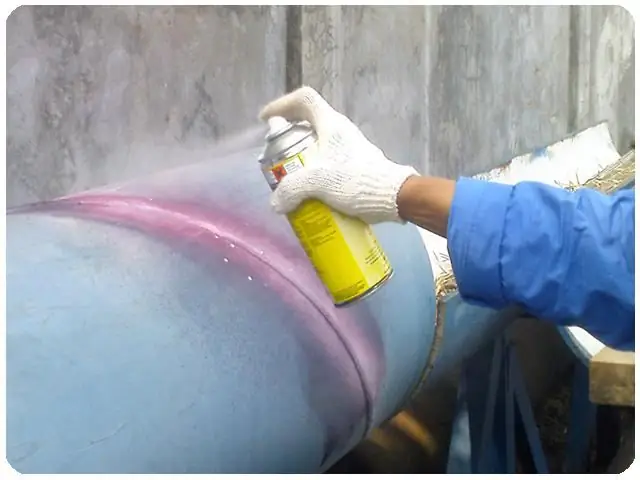
Destination
Capillary flaw detection (i.e. capillary control) is intended for the manifestation of invisible or poorly visible to the naked eye through and surface defects in objectscontrol. This technique allows you to determine their location, extent and orientation on the surface.
Capillary methods of non-destructive testing are based on capillary penetration of the indicator liquid into the cavity of the surface and through material of the object. As part of the application of this technique, the indicator traces formed are registered visually or using a transducer.
Control rules
The capillary testing technique is used to control objects of any size and shape, which are made of non-ferrous and ferrous metals, alloy steel, cast iron, metal coating, plastic and so on. Materials such as glass and ceramics can also be applied in the fields of energy, rocket technology, aviation and shipbuilding. This method, among other things, is also applicable in the construction of nuclear reactors, in the chemical industry, in the field of metallurgy, automotive, electrical engineering, mechanical engineering, foundry, stamping, instrumentation and other industries. For some products and materials, this technique is the only way to determine the suitability of a part or installation for work.
Capillary flaw detection is also used for non-destructive testing of objects that are made of ferromagnetic material, when their magnetic property, shape, type and location of the defect do not allow achieving the sensitivity required by GOST using the magnetic particle method and magnetic particle testing technology.
EssentialThe condition for detecting defects such as discontinuities in the material by capillary methods is the presence of cavities free from all kinds of contaminants and other substances that have access to the surface of objects, and in addition, the depth of propagation, which significantly exceeds the width of their opening. Capillary control is also used in leak detection in conjunction with other methods and in monitoring objects during operation.
What does capillary flaw detection of welds imply? This will be discussed later.
Welds
This method of flaw detection has been known to mankind for a very long time. We can say for sure that even in the Middle Ages, craftsmen used it to detect surface cracks invisible to the naked eye on various products. It is also suitable for conducting a weld inspection.
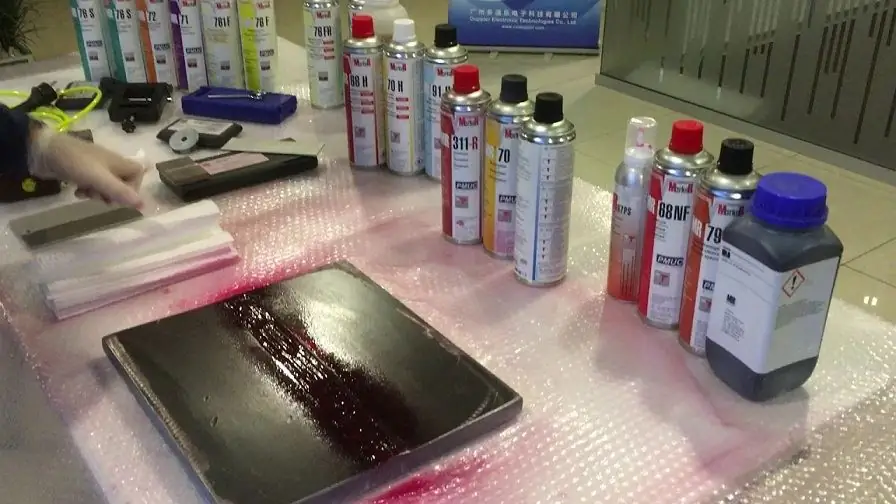
In order to carry out color flaw detection by the capillary method, the prepared part is immersed in a special colored solution, which is often called a penetrant. In this solution, the part is kept for five to ten minutes, and then washed in cold water. When washing is completed, a thin layer of white paint is applied to the controlled surface, it can also be clay. Drying, the solution is absorbed, and the part is painted. A clearly visible pattern appears in the area of the defect.
The benefits of this technique
Such a technique for detecting a defect in welds has become quite widespread, sincehas a number of different important advantages. There is no need for complex equipment. All required materials are usually quite cheap and can be purchased at a standard hardware store.
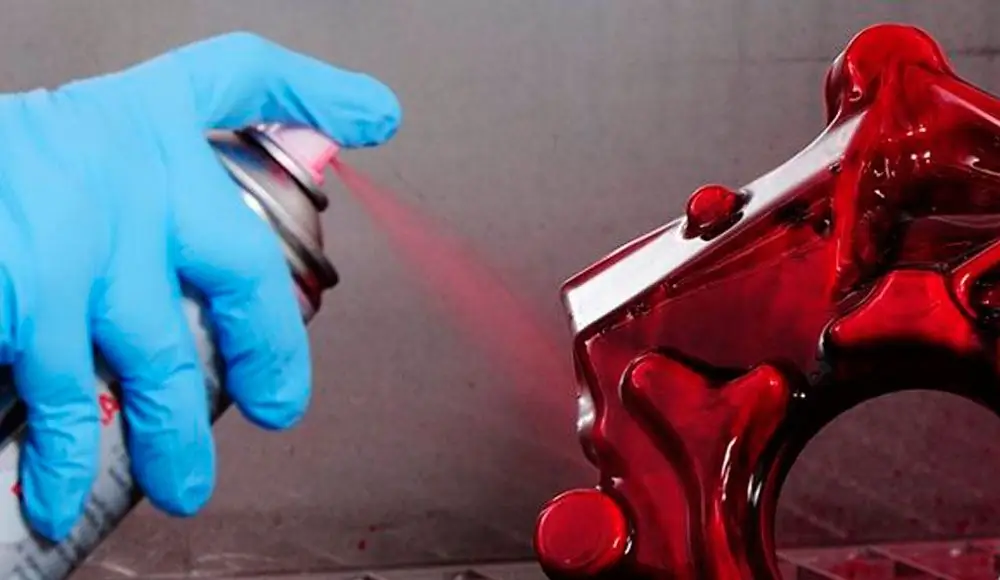
Examination usually doesn't take too long. Thus, this means that such a technology can be used even in mass production. It does not matter at all what the sample for capillary flaw detection is made of. It can, for example, be cast iron or steel along with non-ferrous and non-ferrous alloys, various plastics and even ceramics.
This technique is quite accurate, as it allows you to identify cracks that have a size of one micron. The process of performing color flaw detection is quite simple, and even an ordinary person who does not have special skills is able to master it. Of course, there are various disadvantages that limit the use of such methods of quality control of welds. It is worth noting that there may be an inability to detect a hidden defect and cracks that do not come to the surface. This is important in situations where overall strength requirements are particularly high.
Immediately before starting the inspection, the parts must be thoroughly cleaned of dirt and grease. It is at this stage that the most serious problems can arise. However, they will have to be solved, since otherwise the accuracy of the result obtained may be in great doubt. Considering that bulkyelements of a welded structure, such as a gas pipeline or a building frame, cannot be placed in a tank with a penetrant; during construction, color flaw detection is extremely limited.
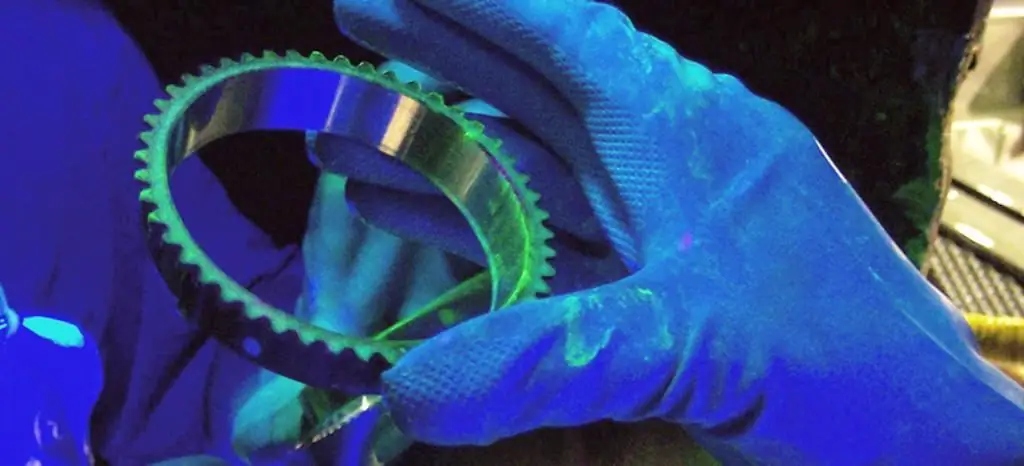
For guaranteed detection of defects, short-term immersion of a control sample for capillary flaw detection in a solution, unfortunately, is not enough. According to the recommendations, the period of such bathing should be about thirty minutes, and therefore a simple technique is recommended to be used only for selective control.
Developer for capillary flaw detection
The control processes start after the developer is finished and last approximately thirty minutes. The presence of color saturation indicates the size of the defect. The lower the color concentration, the smaller the size of the defective area. A more saturated gamma can appear mainly within deep cracks. After completing the control, it is imperative to remove the developer with water or using a special cleaner.
It is due to the effects of the penetrant that complete penetration into the most inaccessible areas of defects is achieved. And the developer, which was applied to the surface of the product, provides a thorough dissolution of the dye located in the internal cavity of the defect. This process allows you to fully understand exactly where the defective areas are located. Against this background, a color trail appears that has a linear appearance, purposefully indicating a crack, scratch or pore.
Whatmaterials for capillary flaw detection are used?
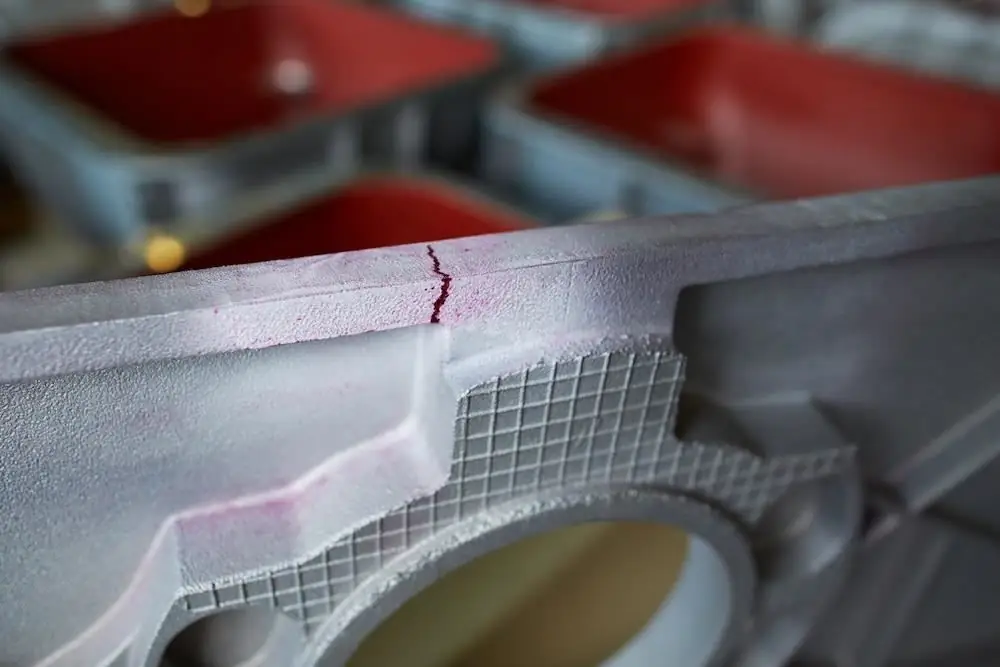
Materials: penetrant
In the process of flaw detection, a penetrant is used. This is a material that has the properties of a flawless capillary effect, which has the ability to penetrate into discontinuous sections of the product, and in addition, has the property of finding the required defects. The penetrant in its composition has substances that have coloring preparations or luminescent additional additives. Such components are an excellent auxiliary link in detecting all kinds of cracks and defective areas.
Kit for capillary flaw detection
Products that are required for color flaw detection are, first of all, luminescent materials from the Ziglo brand. The kits that are needed for capillary control are called Magnaflux, Sherwin and Helling. Spray guns are also used along with hydropneumatic guns, ultraviolet lighting devices, test panels, along with control materials used in color flaw detection.
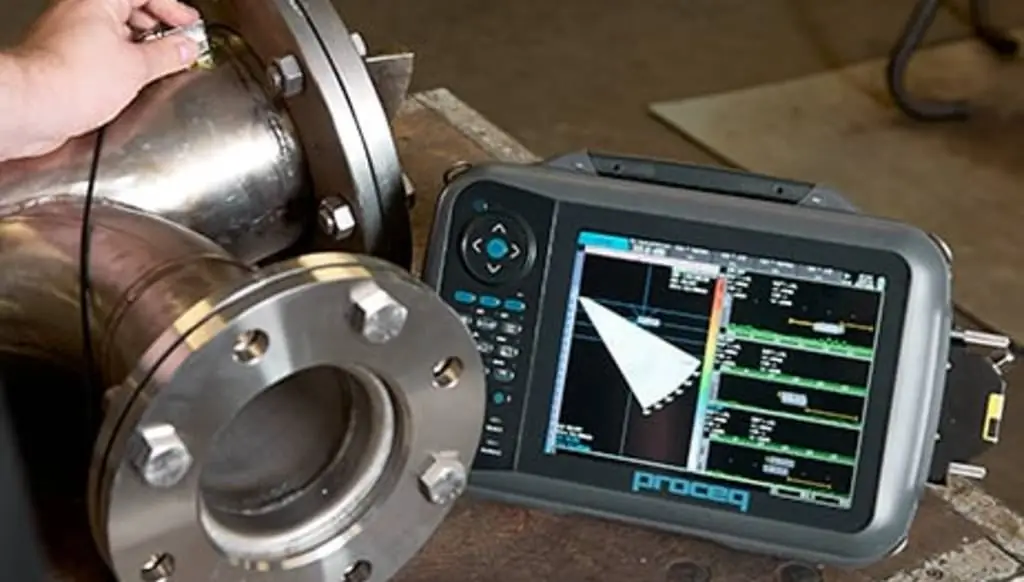
Helpful tips
The color of the dye is usually not too important. The main thing is that it differs in contrast. The current GOST clearly standardizes the degree of illumination in the framework of flaw detection. They are also allowed to use luminescent paints, and for illumination it is recommended to use a light source with a non-translucent reflector. ATIn some situations, the part is heated to obtain a clearer image.
Of course, not all people have vision that allows you to see even bright colored lines only a few microns thick. And in this regard, when working with standards, the use of a magnifying glass and even a microscope is allowed. It should also be added that with the help of the method of color flaw detection, one can not only check the quality of the weld, but also easily detect the joints of parts tightly fitted to each other. This can be extremely important in situations where you have to try to disassemble devices that differ in an unfamiliar design.